1979 Ford Escort RS2000: Our Shed
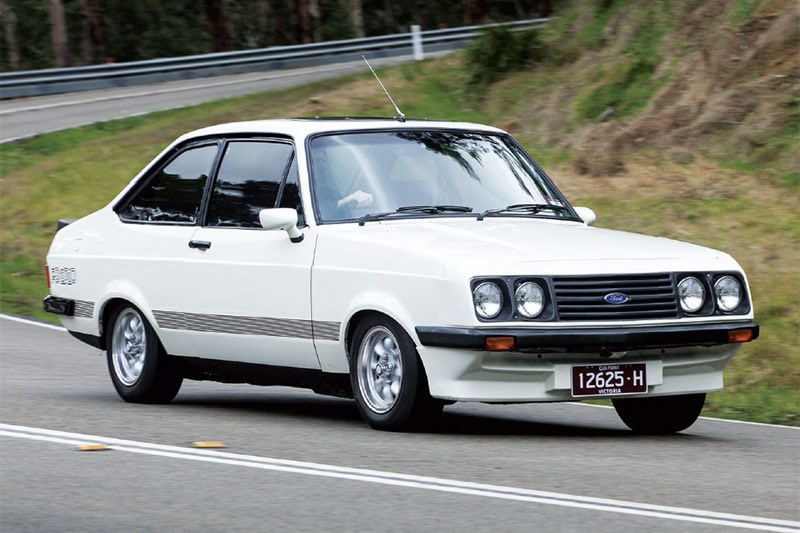
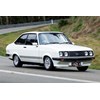
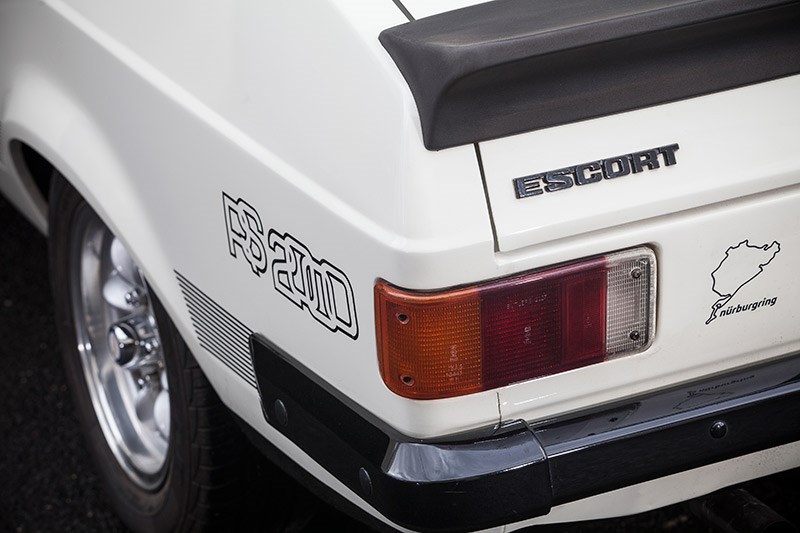
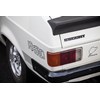
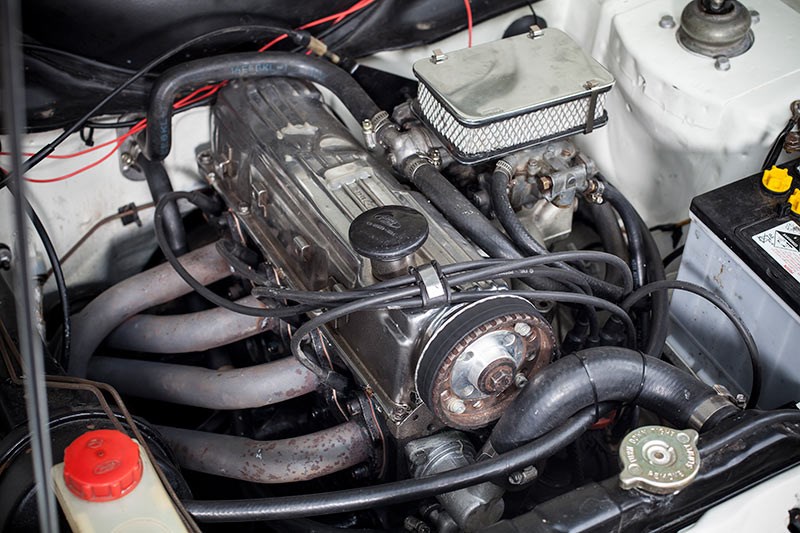
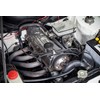
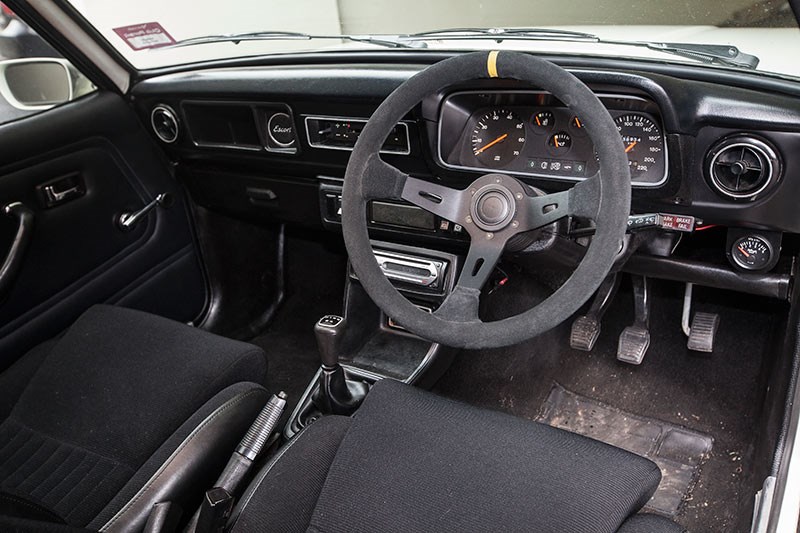
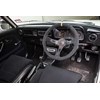
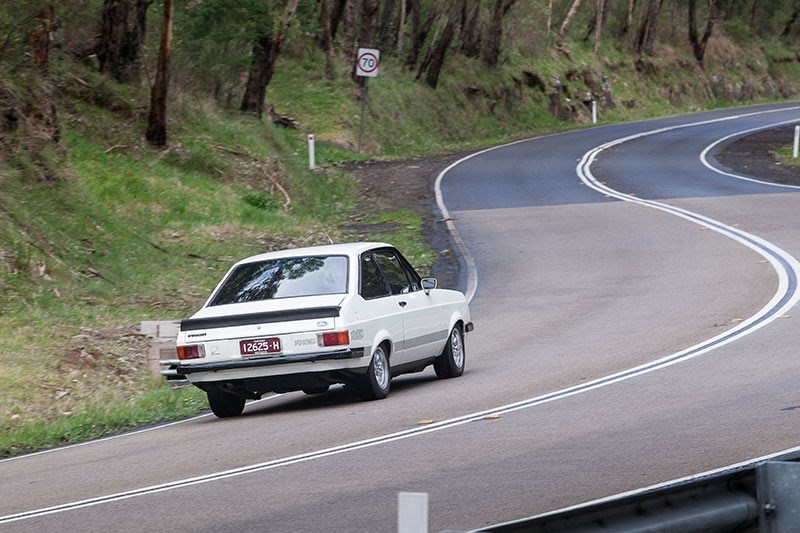
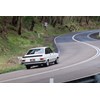
![]() |
![]() |
![]() |
![]() |
![]() |
David Morley gets his RS Escort into gear for competition
Ford Escort RS2000
There’s talk of motorsport in the air. I’ve always loved hillclimbs and there’s the odd speed and single-car event happening these days that’s appealing to me. I don’t want to take the RS2000 circuit racing, because banging doors with 30 other maniacs aint my idea of protecting my precious little Esky. But stuff like a motorkhana or lap-dash where I’m the only car on the track is much more palatable.
In any case, if I’m going to tackle any of this stuff, I need to make a few changes to the car. Safety-related stuff, you understand. An extinguisher with a quick-release catch bolted firmly inside speaks for itself, as does a new set of brake pads. Because I won’t be on track with other hooligans and it’s a closed car (it has a roof) I can forgo the roll-cage and because my car is post-1973 and road-registered (kind of) I can also forget about cutting genuine RS2000 metal for a set of bonnet pins. So far so good.
But what I do need to address are a couple of items that any car in any speed event needs. The first is to lock-wire the various drain plugs, the second is to fit a tailshaft loop.
The engine sump, gearbox and diff all have drain plugs and, should these work loose or – worse – fall out altogether, there’s gonna be a big oily mess on the track and also, potentially, all over my tyres. I wouldn’t be the first punter to have crashed after slipping on his or her own oil. So the idea is to take a length of wire, attach it to the drain plug and then fasten it to something else on the car that won’t move, effectively preventing the drain plug from loosening or turning. Sounds simple, but it aint necessarily so easy.
The first thing to do is prepare the drain plug to accept the lock-wire. There are a couple of ways to do this, starting with drilling a small hole across a corner of the plug. In some cases, you won’t even need to remove the drain plug (which is nice, because I hadn’t long changed the oil in the RS) but you do need to work out in advance where you going to attach the other end of the lock-wire. That’s because the lock-wire should pull the plug in the direction that tightens it. Remember that a lock-wire only works in tension, not compression, so having a wire that doesn’t prevent the plug from turning left (left loosey, righty tighty, remember) isn’t worth two balls of goat poop.
Another method is to weld a washer or tab to the drain plug to secure the lock-wire to, but that only works if you can still get the appropriate spanner or socket on to it to undo it when the time comes. On my car, both the gearbox and diff plugs also serve as the correct level indicators. Basically, when the oil starts dribbling out the holes, you have enough oil inside the box or diff. So as well as giving them a quick level check, removing the drain plugs also meant I could put them in the drill-press to drill them accurately. It’s also worth drilling them twice, at 180-degrees apart, so that where ever they end up when tightened, there’s scope for making the lock-wire run the correct direction to secure them. And don’t be tempted to over or under-tighten a drain plug just so it’s lock-wire hole lines up correctly.
And here’s a trap for young players: Don’t attach the engine drain-plug lock-wire to something like a handy tab in the engine bay or cross-member. The engine moves on its mounts as the load on it changes, so a tight wire from the sump needs to attach to something else on the engine or gearbox which will move in sympathy with the sump plug.
The rest is the easy bit; using a set of lock-wiring pliers to tension the wires and you’re done. And don’t be tempted to use fuse wire or copper stuff; I like soft stainless wire that’s made for the job.
Next job was the tailshaft loop. It all depends where you’re racing and who’s doing the scrutineering as to what you’ll need, but my solution was to bend a strip of 3mm metal around an old muffler as a form (after measuring the tailshaft diameter and the size of the trans tunnel) to produce the loop. Then I welded on two tabs, drilled them to line up with a couple of vacant holes in an underfloor gusset and bingo.
Now, if the front uni joint explodes, the tailshaft can’t drop on to the road and pole-vault me into the next parish. And, happily, the loop is in the exact position to keep the shaft off the deck even if the rear uni goes to lunch.
Time to dust off the helmet.
Unique Cars magazine Value Guides
Sell your car for free right here
Get your monthly fix of news, reviews and stories on the greatest cars and minds in the automotive world.
Subscribe