Morgan factory
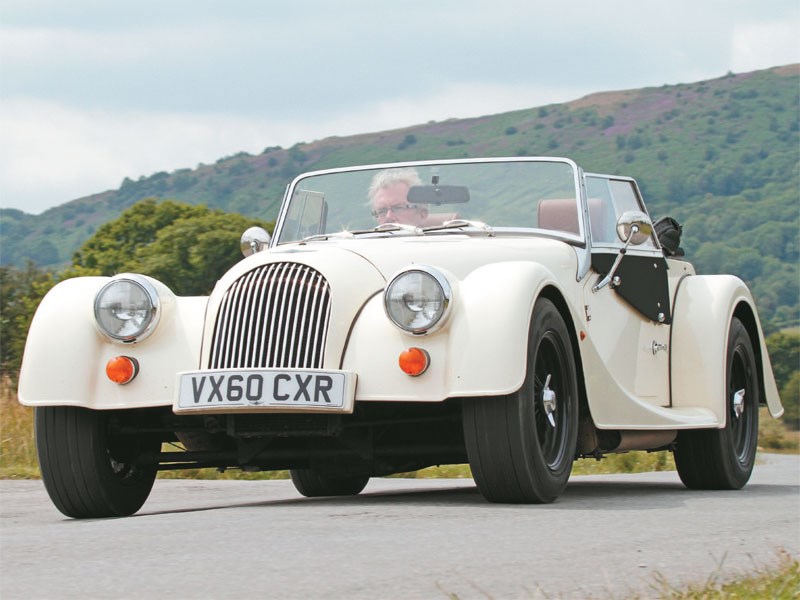
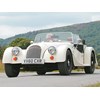
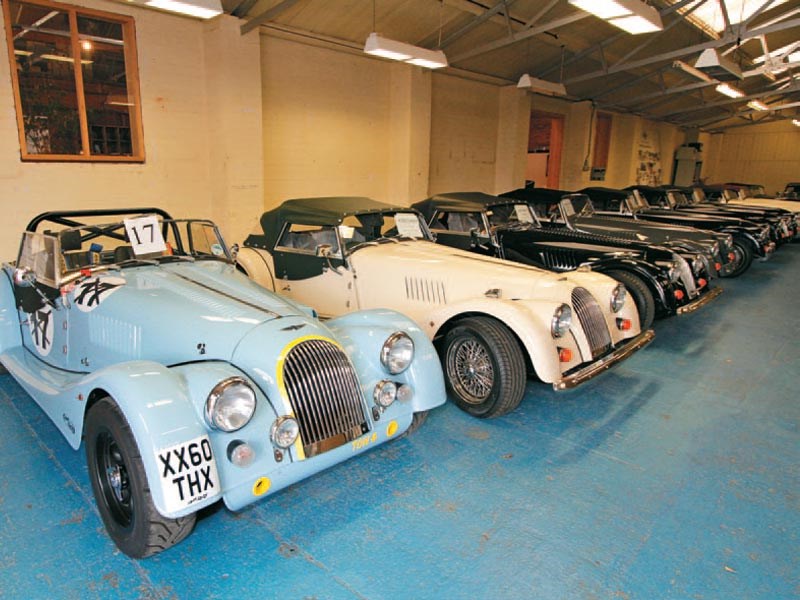
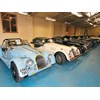
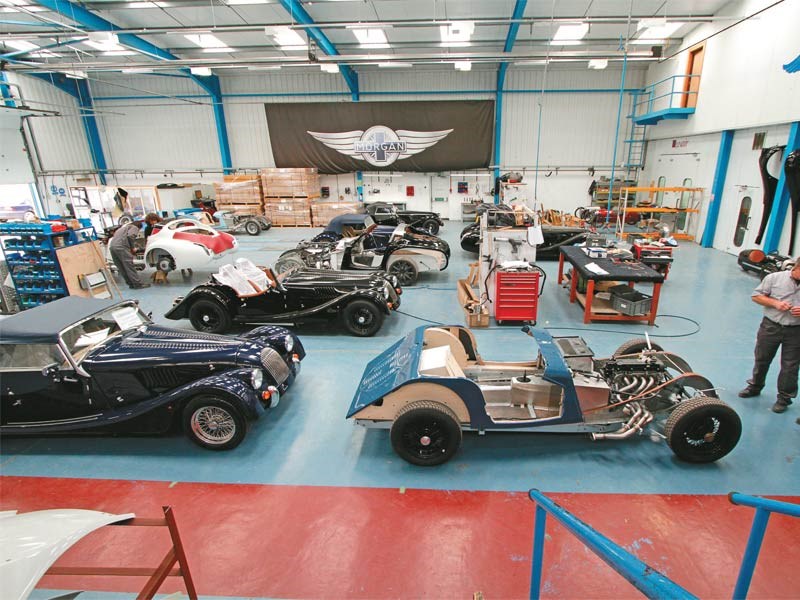
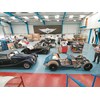
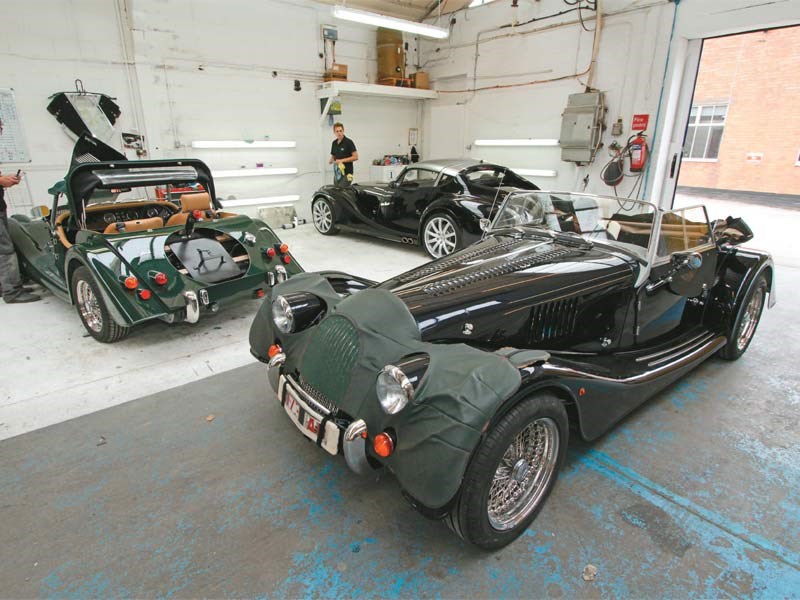
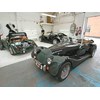
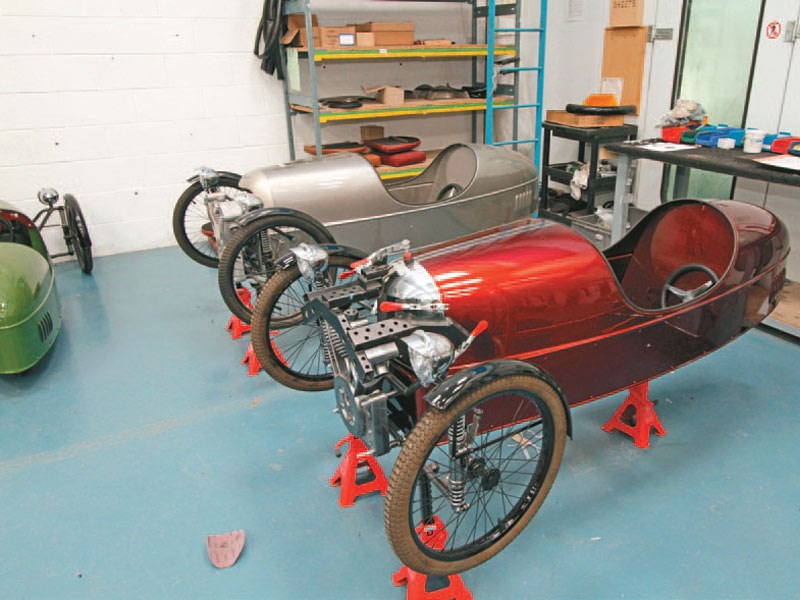
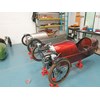
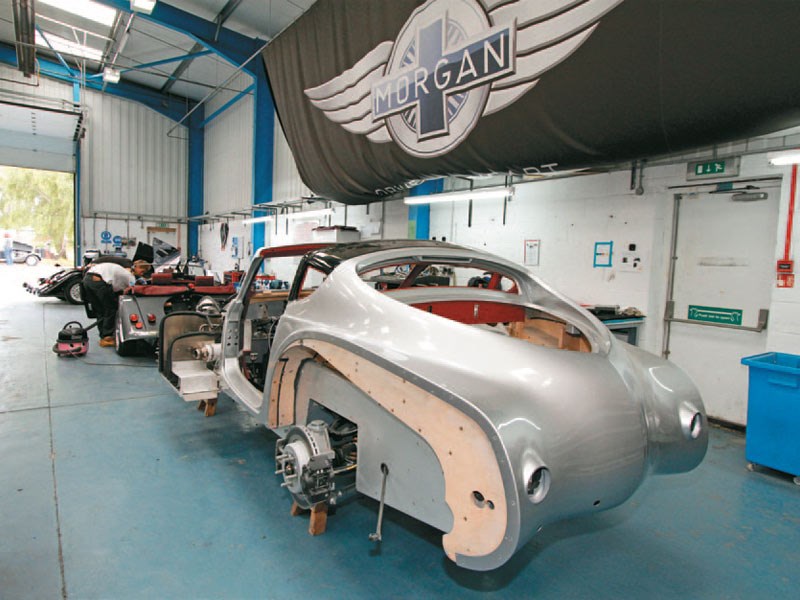
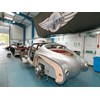
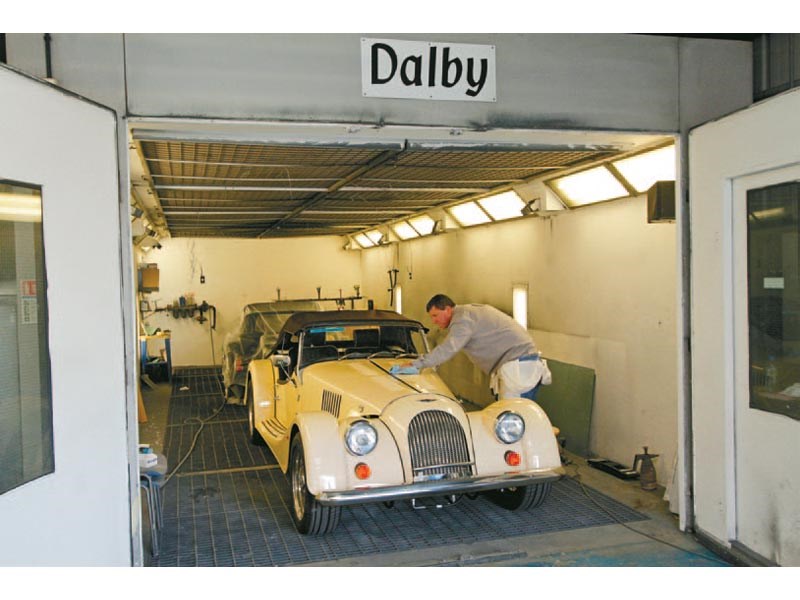
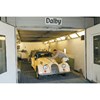
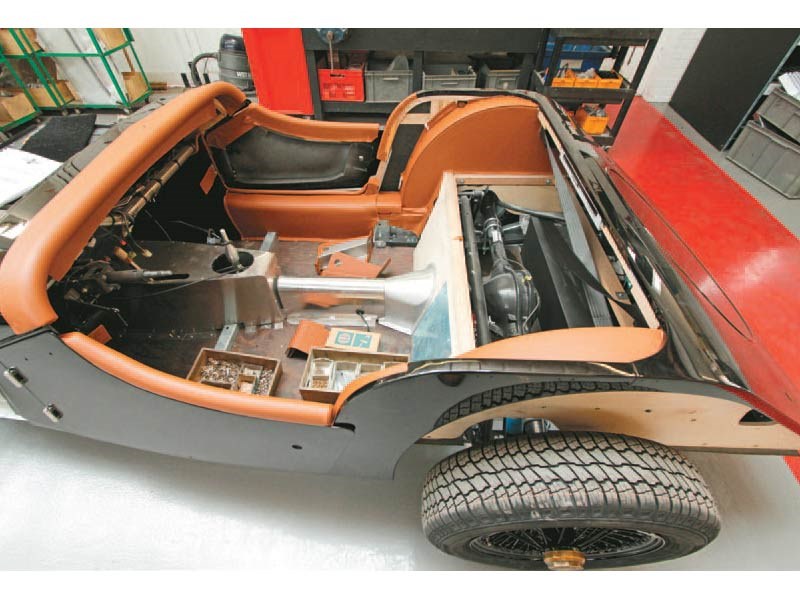
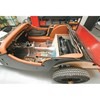
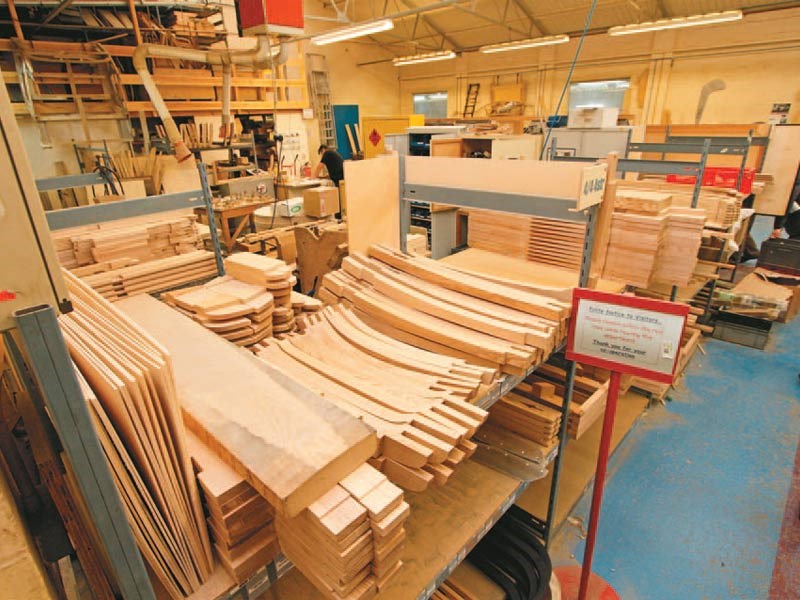
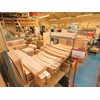
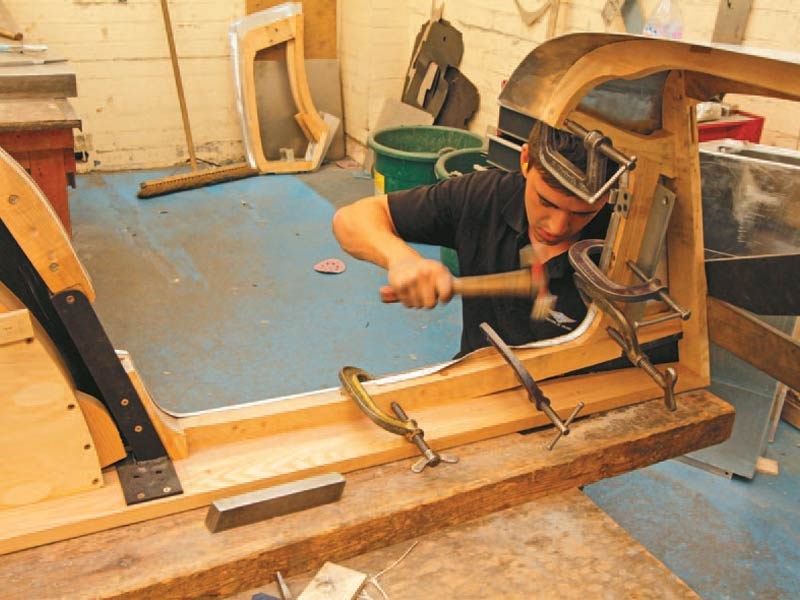
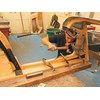
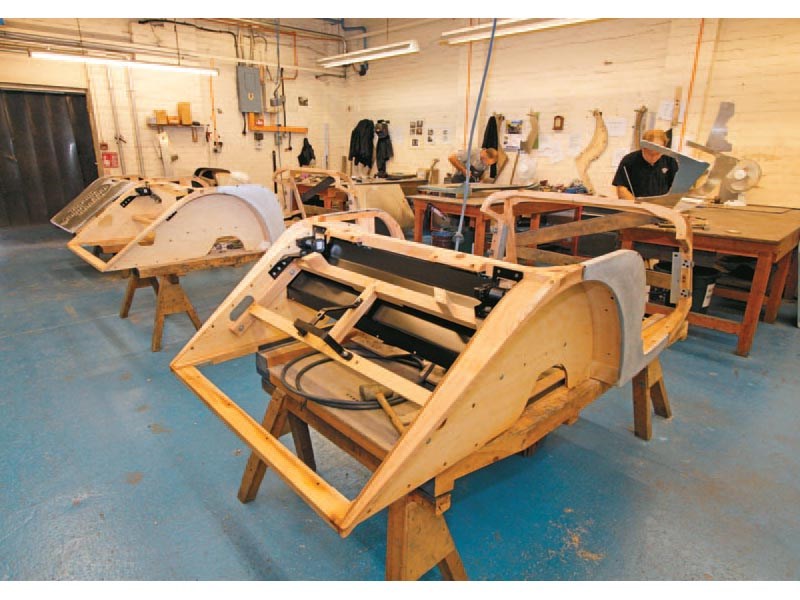
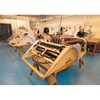
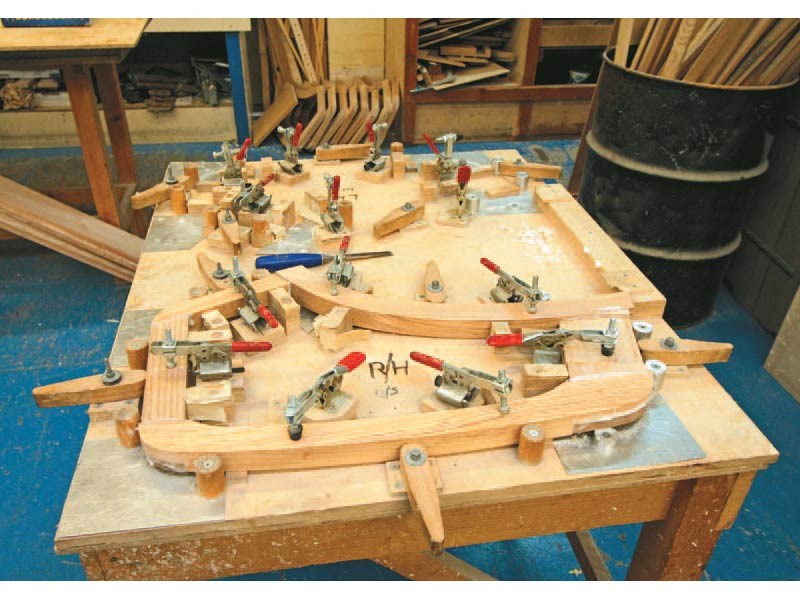
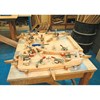
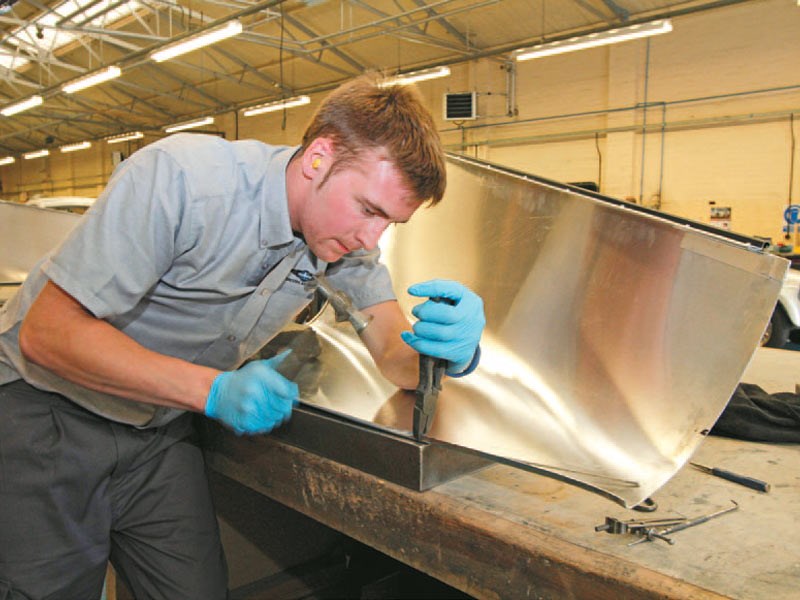
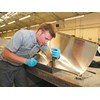
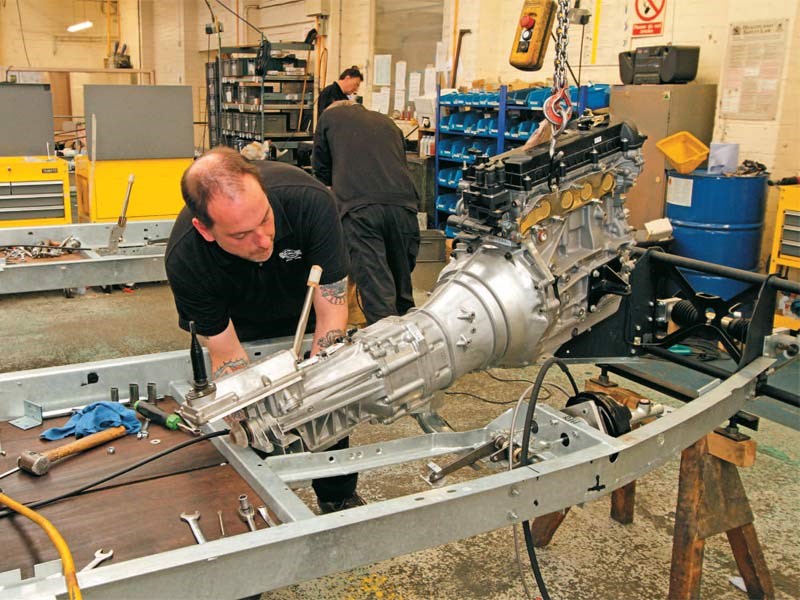
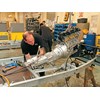
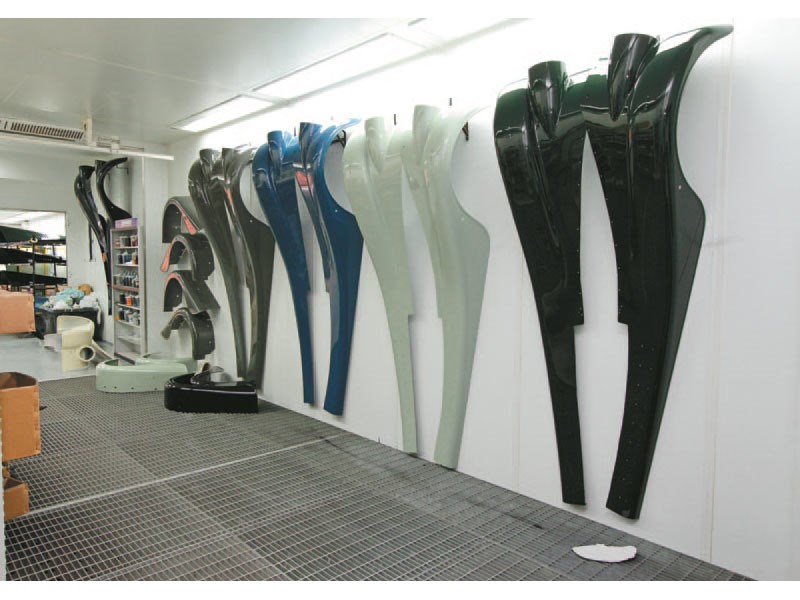
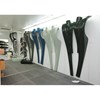
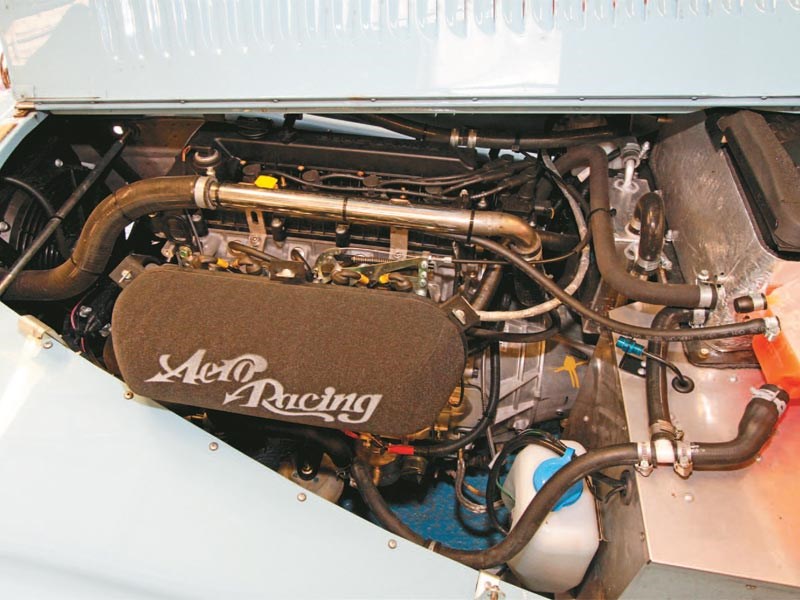
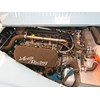
![]() |
Morgan factory
|
![]() |
Morgan factory
|
![]() |
Morgan factory
|
![]() |
Morgan factory
|
![]() |
Morgan factory
|
![]() |
Morgan factory
|
![]() |
Morgan factory
|
![]() |
Morgan factory
|
![]() |
Morgan factory
|
![]() |
Morgan factory
|
![]() |
Morgan factory
|
![]() |
Morgan factory
|
![]() |
Morgan factory
|
![]() |
Morgan factory
|
![]() |
Morgan factory
|
![]() |
Morgan factory
|
More than 100 years on, Morgan shuns today’s Mass production in favour of real craftsManship, and is better for it
![]() |
Morgan factory
|
Morgan factory
Small Wonders
The world might still be teetering on the edge of a financial maelstrom, but nobody seems to have told the fans of Morgan. Its 95-year-old factory on Pickersleigh Road, Malvern, on the far western edge of the British Midlands, is a hive of activity. The air rings with the sound of sheet metal being turned into wings and bonnets, the thud of hammers and saws buzzing, sewing machines singing.
Morgan’s precociously young designer, Matt Humphries, says the company sold 500 of its new ‘3 Wheeler’ model – two year’s worth of production – just months after the car had launched.
In addition to the unique three-wheeler, Morgan is also set to debut the Eva GT four-seater coupe this year, the company’s first global car in its 104-year history.
The traditionalist company proved it can move with the times, too, unveiling a concept car with classic 1940s styling and 21st century EV technology at last year’s Geneva motor show.
We’re standing near a row of 164kW, 2.0-litre specials built to commemorate 60 years of the ‘Plus 4’. Humphries explains how the car has been pared back to its original simplicity with knock-on Minilites, aero screens for racing, louvered rear panel and a Le Mans-style filler cap.
The colours, all taken from the period BMC catalogue, hark to another era: ‘Tartan Red’, ‘Primrose Yellow’, ‘Old English White’, but with the addition of yellow detailing round the grille and air intake echoing "the Astons and 250GTOs of the time," Humphries says.
Morgan’s red brick factory is a throw back to a different era of car assembly, to a time when craftsmanship and pride in a job meant as much as the money at the end of the working week.
That still holds true in many other car makers such as Aston Martin, Bentley and Roll-Royce. The difference, however, is the latter trio use a high degree of technology in assembly processes. Morgan is much more of a cottage industry and none the worse for being so.
The 10-building site hasn’t changed much over the decades, although there’s a relatively new fabricated assembly area at the far end, built specially to produce the ‘AeroMax’. There are no conveyor lines or robots and, famously, the rolling chassis’ are pushed from one station to the next. In something of a minor manufacturing revolution, Morgan reorganised its manufacturing process and employs gravity so the cars are now pushed downhill from chassis assembly to final.
Visiting car factories these days usually entails a health-and-safety briefing before donning high-vis jackets, safety goggles and ear plugs, while being carefully escorted by a guide. Not so with Morgan.
With a wave, Humphries heads back to his four-person design department, including an intern. "I’ll see you when you’ve finished – just follow the red line – you know your way round anyway."
The faded red path is testament to the hundreds of visitors Morgan receives weekly from around the world, eager to see their cars being built or just curious enthusiasts.
Increasing demand has meant Morgan adopting streamlined production processes and maximising efficiencies for the 20,000-odd parts required each month to maintain production momentum.
Despite an unlimited colour palette to choose from, the cars have a restricted list of paint and trim options to simplify production. Still, Morgan provides numerous dashboard configurations in leftor right-hand drive, and imperial or metric instrumentation. This is accentuated with the sight of crated BMW and Ford engines and transmissions throughout the factory awaiting installation into various models.
It’s a six-stage process to build a Morgan: chassis, assembly, sheet metal work, wood, machine, and paint and trim.
Chassis assembly takes place at the top of the site, to the sound of metal bashing and hand forming, while the powertrain, suspension, steering and wiring harness are installed to create a rolling chassis. Each car has its own build book, detailing all the components and quality sign off at each stage of the assembly.
The raucous din of the metal shop quickly gives way to the sound of saws and the sweet aroma of sawdust as the car’s ash-frames are individually assembled by one carpenter. Each frame uses about three square metres of timber and takes some 13 hours to assemble. A mixture of traditional and vacuum presses ease the bonded wood into light, yet extremely resilient forms.
"The beauty of using timber is that it can be exposed and used as a styling effect, as well as a functional component," Humphries says. "There’s purity to that functionality which other manufacturers have lost by twisting veneers into complex forms that wood naturally cannot achieve."
Even Rolls-Royce sent its design team to Malvern to learn what Morgan does.
Aluminium wings, doors and other body panels – all hand-formed, except in the case of the Aero SuperSport, which is produced off site using a process known as "super plastic-form aluminium" – gradually clothe the skeletal ash frame before it is sent to the paint shop.
Leather and cloth trims are hand cut and sewn for the seats and interior, and await final assembly prior to a final road test, pre-delivery inspection and under-seal.
Finished cars await shipment, or collection by eager owners back at the top of the site, not far from where our tour started. As with every day at Pickersleigh Road, there seems to be almost as many visitors as there are employees.
Current managing director and Grandson of the company founder, H. F. S. Morgan, Charles Morgan, regularly speaks of the extended Morgan ‘family’. Employees, dealers and owners all share a common enthusiasm for the brand that exceeds nationality and language.
With an estimated 25,000 Morgan cars on the road today, it may seem like a big extended family. But in this era of mass production, it’s a mere pin-prick, a rarity, and all the better for it.
Unique Cars magazine Value Guides
Sell your car for free right here
Get your monthly fix of news, reviews and stories on the greatest cars and minds in the automotive world.
Subscribe